The Immense Benefits of Plastic Injection Molding in Modern Business
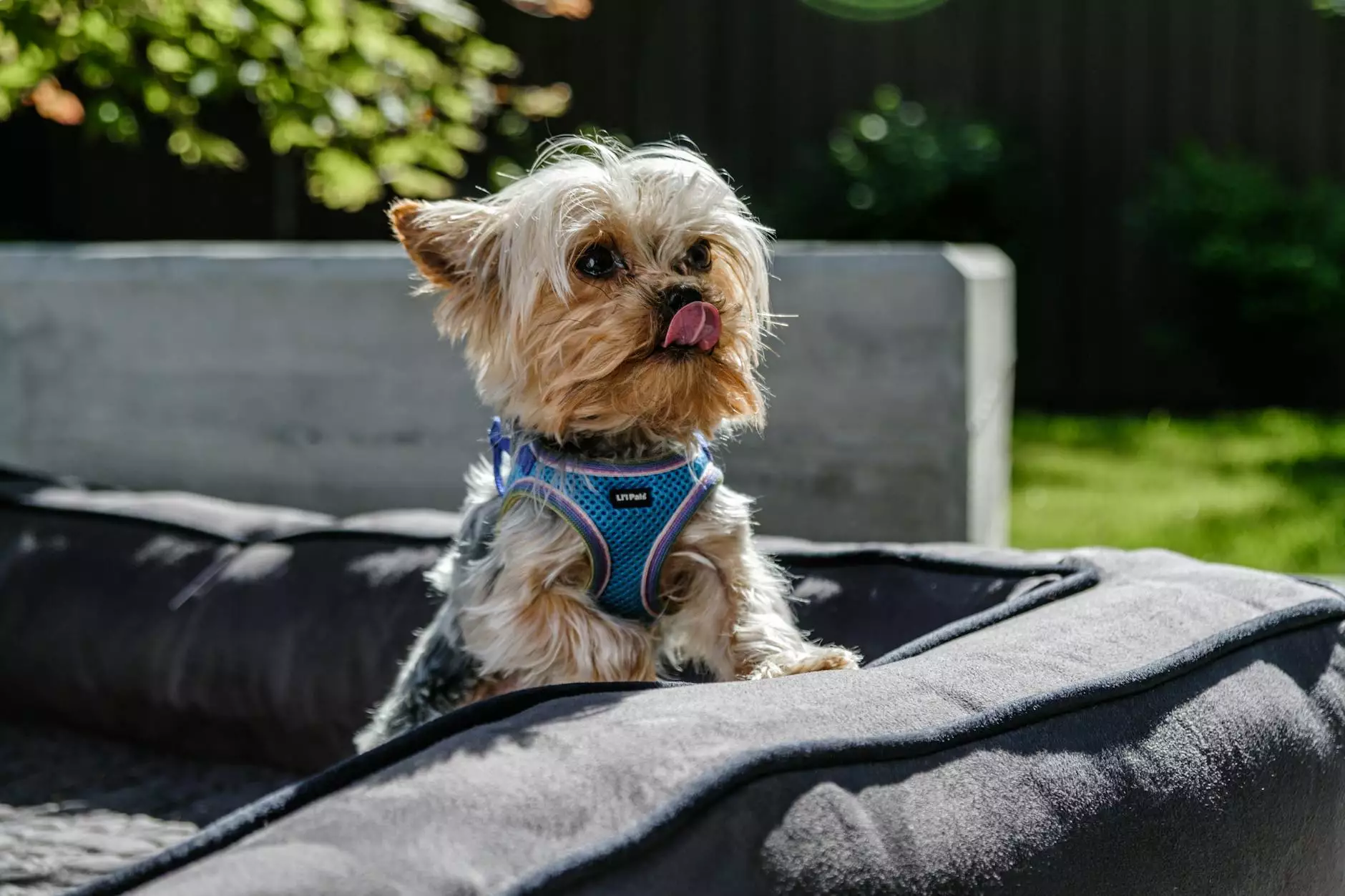
Plastic injection molding has become a cornerstone technology in the manufacturing sector, providing businesses with the ability to produce intricate parts efficiently and at scale. This article delves deep into the world of plastic injection molding, exploring its advantages, applications, and its transformative impact on business operations, particularly in the realm of metal fabricators, like those found at deepmould.net.
Understanding Plastic Injection Molding
At its core, plastic injection molding is a manufacturing process used to create parts by injecting molten plastic into a mold. The process involves the following steps:
- Material Selection: The first step involves choosing the right type of plastic, depending on the desired properties of the final product.
- Mold Creation: Skilled engineers design a mold that will define the shape of the final product. This requires precision and expert knowledge, particularly in a field like metal fabrication.
- Melting the Plastic: The chosen plastic resin is heated until it becomes molten.
- Injection into the Mold: The molten plastic is injected into the mold at high pressures, ensuring that it fills every cavity.
- Cooling and Solidification: The plastic is allowed to cool and solidify into the desired shape.
- Mold Removal: Finally, the newly formed part is ejected from the mold, ready for further processing or finishing.
Why Choose Plastic Injection Molding?
The advantages of adopting plastic injection molding in manufacturing processes are vast. Here are some compelling reasons:
1. Efficiency and Speed
Thanks to the automated nature of injection molding, businesses can produce thousands of units in a fraction of the time it would take with traditional manufacturing methods. This is particularly beneficial for metal fabricators who require precision parts at scale.
2. Flexibility in Design
Injection molds can be designed for a myriad of shapes and sizes, allowing for complex geometries that might be impossible with other techniques. This flexibility is essential for companies looking to innovate or customize their product lines.
3. Consistent Quality
Once a mold is created, the parts produced are highly uniform, drastically reducing the margin for human error and enhancing overall product quality. This consistency is critical for maintaining reputation and meeting customer expectations.
4. Cost-Effectiveness
While the initial investment in mold design and production may be high, the efficiency and volume of production significantly reduce the cost per unit, making it an economically viable option for businesses of all sizes.
Applications of Plastic Injection Molding
The applications of plastic injection molding are virtually limitless, with industries ranging from automotive to consumer goods benefiting from this technology:
- Automotive Industry: Production of dashboards, instrument panels, and other interior components.
- Medical Devices: Creation of sterile components that require precision and reliability.
- Consumer Electronics: Manufacturing cases and components for smartphones, laptops, and other devices.
- Household Goods: Production of items such as containers, utensils, and furniture fittings.
- Toys: Creating varied toys with intricate designs that are safe and durable.
The Role of Metal Fabricators in Injection Molding
Metal fabricators play a crucial role in the injection molding process. They provide the necessary molds that are critical for the success of any injection molding operation. High-quality molds are essential for the following reasons:
1. Precision Engineering
Metal fabricators employ advanced technologies to create molds that perfectly match the specifications of the desired parts. This precisiveness is crucial for industries where tolerances are tight and imperfections can lead to significant issues.
2. Durability and Longevity
High-quality metal molds can withstand the high pressures and temperatures involved in injection molding, resulting in a longer lifespan and reduced costs over time.
3. Customized Solutions
Many businesses require unique solutions for their specific needs. Skilled fabricators can create custom molds tailored to unique product designs, ensuring that every aspect of the mold fits the client's vision and production needs.
4. Innovation in Materials
With ongoing advancements in metal materials and coatings, fabricators can offer innovations that enhance mold performance, such as improved release properties and greater resistance to wear.
Challenges in Plastic Injection Molding
While there are numerous advantages to plastic injection molding, it is not without its challenges. Understanding these challenges can help businesses prepare adequately:
1. High Initial Cost
The upfront cost of creating molds is often significant, which can deter smaller businesses from pursuing injection molding as a manufacturing option. However, this cost dividends over time through efficiency and volume.
2. Design Limitations
Certain designs may not be feasible with injection molding. It’s crucial to consider the limitations when designing components to ensure manufacturability.
3. Time for Mold Creation
While production times are short, the time taken to create high-quality molds can be considerable, requiring patience from businesses before they see any return on investment.
Future Trends in Plastic Injection Molding
The landscape of plastic injection molding is constantly evolving with trends that indicate the future direction of the industry:
1. Sustainable Practices
As the global focus shifts towards sustainability, many manufacturers are exploring eco-friendly materials and practices in injection molding. Recycled plastics and biodegradable materials are increasingly being integrated into production processes.
2. Smart Manufacturing
The integration of IoT technology in injection molding processes is becoming popular. Smart machines that provide real-time data can optimize production, reduce downtime, and improve decision-making.
3. Advanced Materials
The development of new polymers that provide enhanced performance characteristics is paving the way for creating complex parts that were previously unachievable.
4. Regionalization of Manufacturing
Businesses are beginning to recognize the advantages of regional manufacturing to reduce lead times and improve customer service by establishing local production facilities.
Conclusion
In summary, plastic injection molding is a game-changer in the manufacturing industry, providing unparalleled benefits in efficiency, precision, and cost-effectiveness. The contributions of skilled metal fabricators cannot be overstated, as they lay the foundation for the success of this technology. As the industry continues to evolve, businesses that embrace the longevity, flexibility, and innovation offered by injection molding will undoubtedly find themselves positioned for success in the competitive marketplace.
For businesses looking to maximize their manufacturing capabilities, consider partnering with experienced professionals in metal fabrication and plastic injection molding to ensure high-quality production and efficient operations.