The Impact of Plastic Molding Injection in Metal Fabrication
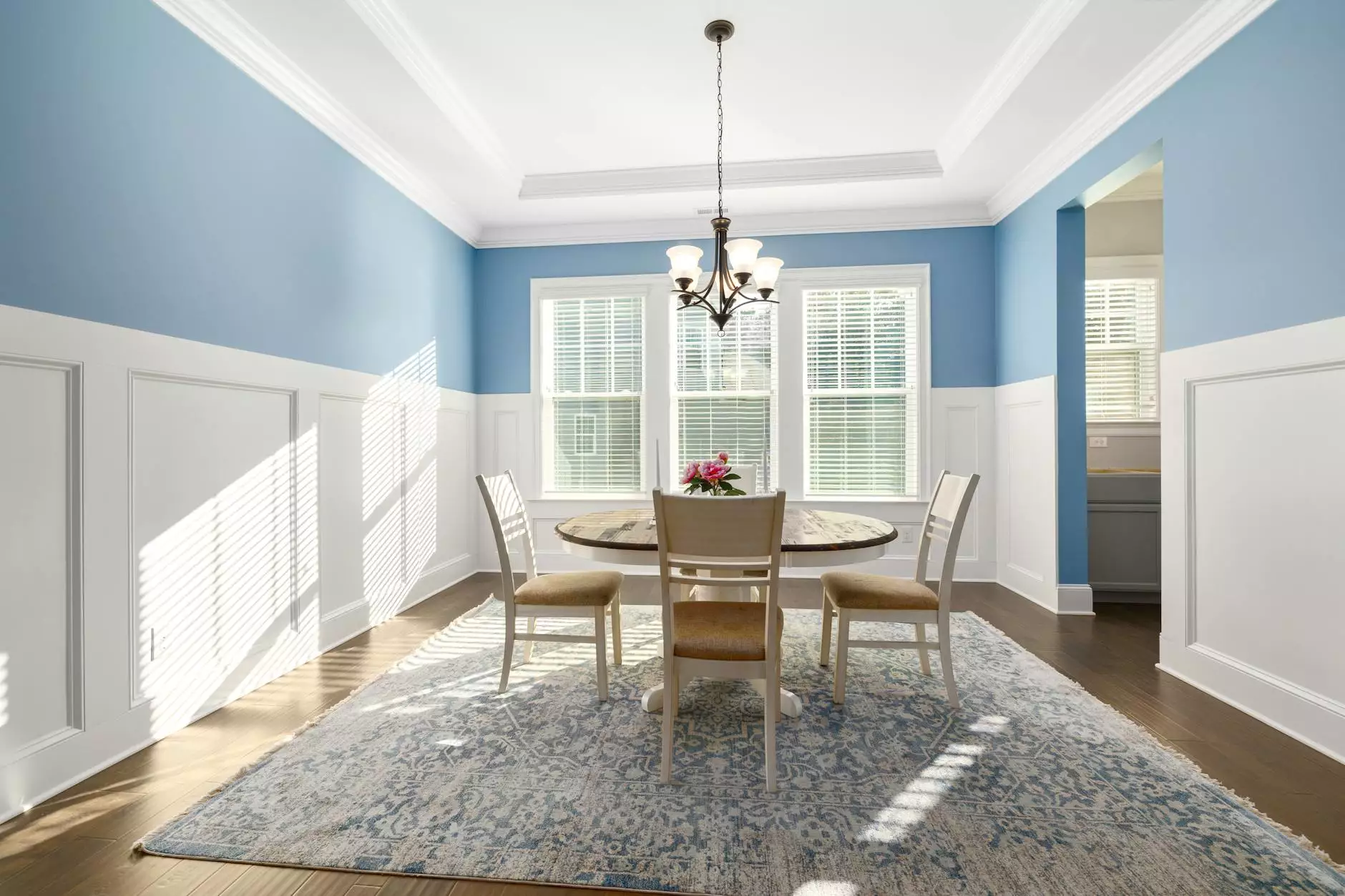
The integration of plastic molding injection in the metal fabrication industry is a transformative step that many businesses have embraced in recent years. This process not only enhances production efficiency but also offers remarkable benefits in terms of cost-effectiveness, precision, and versatility. In this article, we will delve deep into what plastic molding injection is, its processes, advantages, and its far-reaching implications for the metal fabrication sector.
What is Plastic Molding Injection?
Plastic molding injection is a manufacturing process used to create plastic parts by injecting molten plastic into a mold. This method has gained popularity due to its ability to produce complex shapes that would be difficult or impossible to achieve with other methods. The process involves several stages, each critical to ensuring the final product meets high standards of quality and precision.
Stages of Plastic Molding Injection
- Material Selection: The process begins with the selection of suitable plastic materials, which can vary based on the final application of the part.
- Mold Design: Engineers design molds that are precisely crafted to form the desired shape of the plastic part.
- Injection Process: Molten plastic is injected into the mold under high pressure, allowing it to fill every cavity.
- Cooling and Solidification: Once the mold is filled, the plastic cools and solidifies, retaining the shape of the mold.
- Mold Removal: The solidified part is then removed from the mold, ready for any additional processing or finishing.
Advantages of Plastic Molding Injection
The utilization of plastic molding injection in metal fabrication brings with it a plethora of advantages that can significantly enhance manufacturing processes:
Cost Efficiency
One of the primary reasons businesses adopt plastic molding injection is the cost efficiency it offers. The process allows for high-volume production with lower unit costs, making it ideal for mass production runs.
Precision and Consistency
Plastic molding injection provides unparalleled precision and consistency. Each part produced is virtually identical to the next, ensuring quality control across large batches. This high degree of accuracy is essential for components that require tight tolerances.
Material Versatility
This process accommodates a wide range of materials, enabling manufacturers to choose plastics that best meet their application needs, whether for strength, flexibility, or resistance to chemicals.
Complex Designs
Modern mold-making technology allows for intricate designs and geometries that can be produced efficiently. This opens up new possibilities in product development and innovation.
Reduced Waste
Plastic molding injection is environmentally friendly due to its efficiency, resulting in reduced waste material compared to traditional machining processes.
Applications of Plastic Molding Injection in Metal Fabrication
The versatility of plastic molding injection has led to a wide array of applications in the metal fabrication industry. Here are several notable examples:
Automotive Components
Many automotive parts, such as dashboards, bezels, and interior trims, are fabricated using plastic molding injection. The ability to create complex shapes while adhering to strict industry standards makes this process integral to automotive manufacturing.
Consumer Electronics
In consumer electronics, housings for devices like smartphones and tablets are often made through this method, ensuring they are lightweight and durable.
Medical Devices
The medical industry relies heavily on plastic molding injection for producing components like syringes and surgical instruments, where sterility and precision are paramount.
Industrial Parts
Industrial applications also benefit from this process, such as gears, handles, and various structural components that must withstand heavy use.
Challenges in Plastic Molding Injection
While plastic molding injection offers numerous benefits, it is not without its challenges. Understanding these challenges can help improve processes and outcomes:
High Initial Costs
The upfront investment in molds can be substantial, which may deter some manufacturers, especially small businesses. However, this is often offset by lower production costs over time.
Technical Expertise Required
To optimize the injection molding process, skilled personnel are needed to manage mold design, machine operation, and quality control. This requirement adds a layer of complexity to the process.
Material Limitations
Not all materials are suitable for injection molding. Certain plastics may not perform well under specific conditions, limiting options for some applications.
The Future of Plastic Molding Injection in Metal Fabrication
The future of plastic molding injection in the metal fabrication industry is promising. With advancements in technology, such as 3D printing and automation, the efficiency and capabilities of this process continue to expand. Future prospects include:
Increased Automation
As technology evolves, more facilities are adopting automated systems that can streamline the injection molding process, reducing labor costs and enhancing speed.
Sustainable Practices
Environmental concerns are pushing manufacturers towards sustainable plastics and improved recycling processes. Innovations in plastic molding injection are likely to align with these sustainability goals.
Integration with Other Technologies
The fusion of injection molding with other manufacturing processes, such as metal fabrication techniques, will enable the creation of hybrid components that leverage the best of both worlds.
Conclusion: Embracing the Benefits of Plastic Molding Injection
In conclusion, firms within the metal fabrication sector must consider the integration of plastic molding injection into their production processes. The advantages of cost savings, design flexibility, and high-volume production capabilities make it a compelling choice. By staying informed of the latest innovations and addressing associated challenges, businesses can leverage this technology to enhance their operations and maintain a competitive edge in the marketplace.
For companies looking to stay ahead in the evolving landscape of manufacturing, adopting plastic molding injection could be the key to unlocking new opportunities and achieving sustainable growth.