Comprehensive Guide to **Pressure Vessel Inspection**
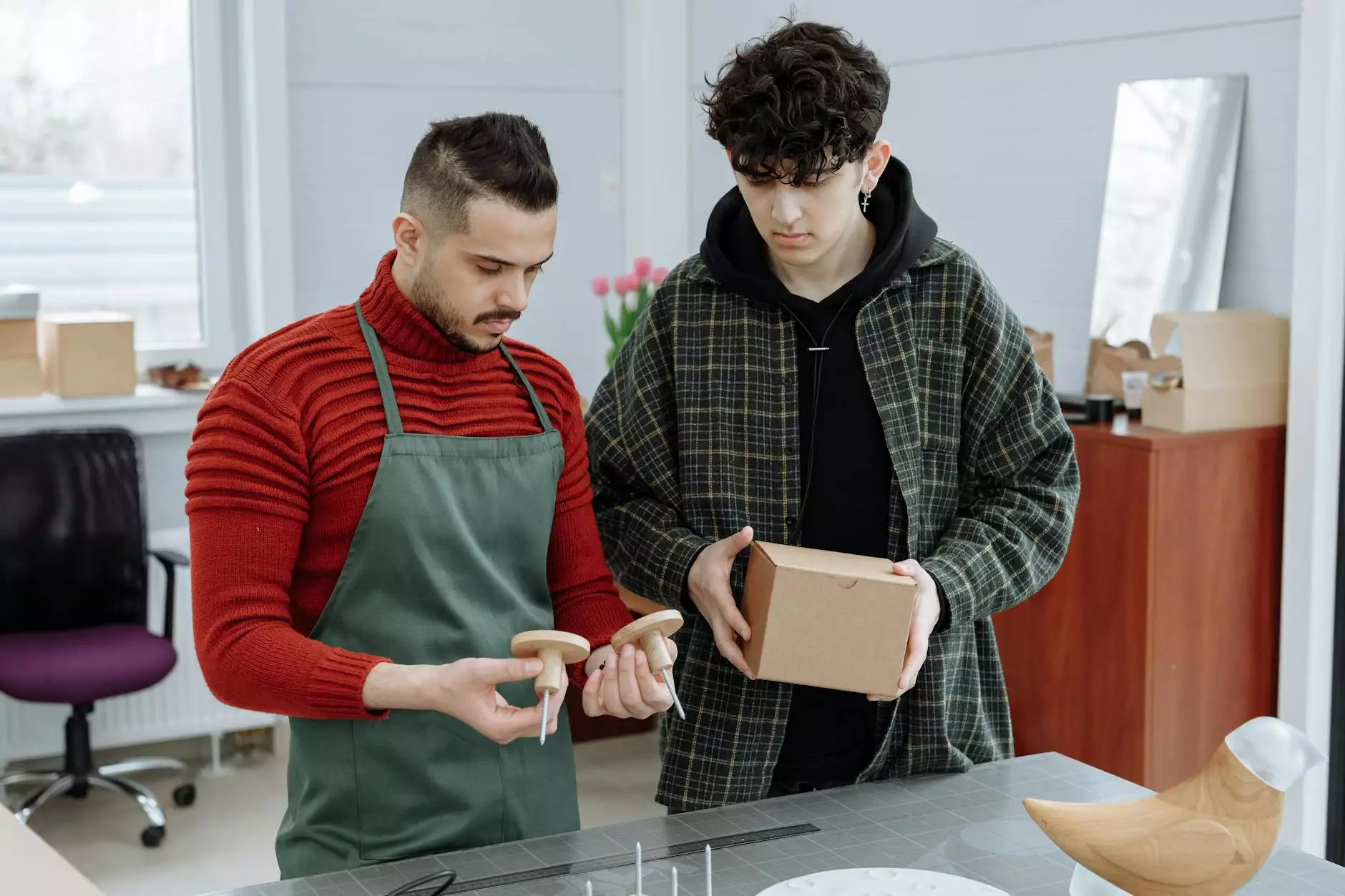
When it comes to ensuring safety and compliance in industrial processes, the significance of pressure vessel inspection cannot be overstated. This extensive guide aims to delve deep into the world of pressure vessels, the importance of regular inspections, the methodologies employed, and the regulatory landscape that governs them. It is paramount for businesses in sectors such as oil and gas, chemical manufacturing, and pharmaceuticals to uphold rigorous inspection standards to avoid catastrophic failures and maintain operational integrity.
What are Pressure Vessels?
A pressure vessel is a container designed to hold gases or liquids at a pressure substantially different from the ambient pressure. Common examples include:
- Boilers
- Storage tanks
- Heat exchangers
- Reactors
Due to their operational nature, these vessels are critical components in many industrial processes and are subject to strict safety guidelines.
The Importance of Pressure Vessel Inspection
Regular and rigorous pressure vessel inspections are paramount for several reasons:
- Safety: The primary reason for conducting these inspections is the safety of personnel and the environment.
- Regulatory Compliance: Adherence to national and international regulations is mandatory to operate legally.
- Operational Efficiency: Regular inspections can help identify potential issues before they escalate, reducing downtime.
- Cost Savings: Early detection of problems can save businesses significant money in repairs and lost productivity.
Regulations Governing Pressure Vessel Inspection
In the UK, pressure vessel inspections are governed by regulations such as the Pressure Systems Safety Regulations 2000 (PSSR) and the Pressure Equipment Directive (PED). These regulations set out requirements for:
- Risk assessment
- Maintenance of pressure systems
- Periodic inspection and testing
Compliance with these regulations is not just a legal requirement; it fosters a culture of safety and accountability within organizations.
Methods of Pressure Vessel Inspection
There are several inspection methods used to assess the integrity of pressure vessels. Each method has its unique advantages and is deployed based on the specific needs of the vessel and its operating conditions:
Visual Inspection
Visual inspection is often the first step in the inspection process. Inspectors look for signs of:
- Corrosion
- Cracks
- Dents
- Leaks
This method, while simple, can provide valuable insights into the overall condition of the vessel.
Nondestructive Testing (NDT)
Nondestructive testing includes several techniques that allow inspectors to assess materials and structures without causing any damage. Common NDT methods include:
- Ultrasonic Testing: Uses high-frequency sound waves to detect imperfections.
- Magnetic Particle Testing: Primarily used for detecting surface and near-surface defects in ferromagnetic materials.
- Dye Penetrant Testing: Reveals surface defects by applying a dye that penetrates cracks.
Pressure Testing
This method involves filling the vessel with a liquid (usually water) and pressurizing it beyond its normal operating pressure to check for leaks and weaknesses. It is a critical part of ensuring the vessel can handle its intended pressure levels safely.
Documentation and Reporting
After conducting pressure vessel inspections, it is essential to maintain comprehensive documentation. Accurate records serve multiple purposes:
- Compliance: Demonstrates adherence to safety and regulatory standards.
- Reference: Provides historical data for future inspections and assessments.
- Maintenance Planning: Facilitates effective scheduling and resource allocation for maintenance activities.
Choosing the Right Inspection Service Provider
Partnering with a qualified inspection service provider is vital for effective pressure vessel inspections. Consider the following when choosing a provider:
- Experience: Look for companies with a solid track record in the industry.
- Qualifications: Ensure that inspectors hold relevant certifications and training.
- Technology: A provider that uses advanced technology can offer more accurate and reliable results.
- Reputation: Seek testimonials and reviews from previous clients to gauge their reliability and quality of service.
The Future of Pressure Vessel Inspection
As technology advances, so too do the methods of pressure vessel inspection. Emerging technologies such as artificial intelligence and machine learning are starting to play significant roles in predictive maintenance and risk assessment. These innovations promise:
- Enhanced Safety: More accurate predictions of potential failures.
- Cost Efficiency: Reduced inspection times and lower operational costs.
- Improved Compliance: Streamlined reporting and documentation processes.
At SafePlant UK, we are committed to providing top-notch pressure vessel inspection services that adhere to the highest safety and quality standards. Our team of experts utilizes the latest technologies and methodologies to ensure your vessels operate without risk, ultimately contributing to the overall success of your business.
Conclusion
In conclusion, the role of pressure vessel inspections in ensuring the safety and efficiency of industrial operations cannot be overlooked. Regular inspections, combined with adherence to regulations and the right methodologies, safeguard not just the assets of a company but also the lives of its employees and the environment. By investing in thorough inspections and maintenance, businesses can ensure a reliable and safe operating environment, thus paving the way for sustained growth and productivity.
For more information about our pressure vessel inspection services and how we can assist you, visit SafePlant UK today.