Understanding Injection Molding Manufacturers: A Comprehensive Guide
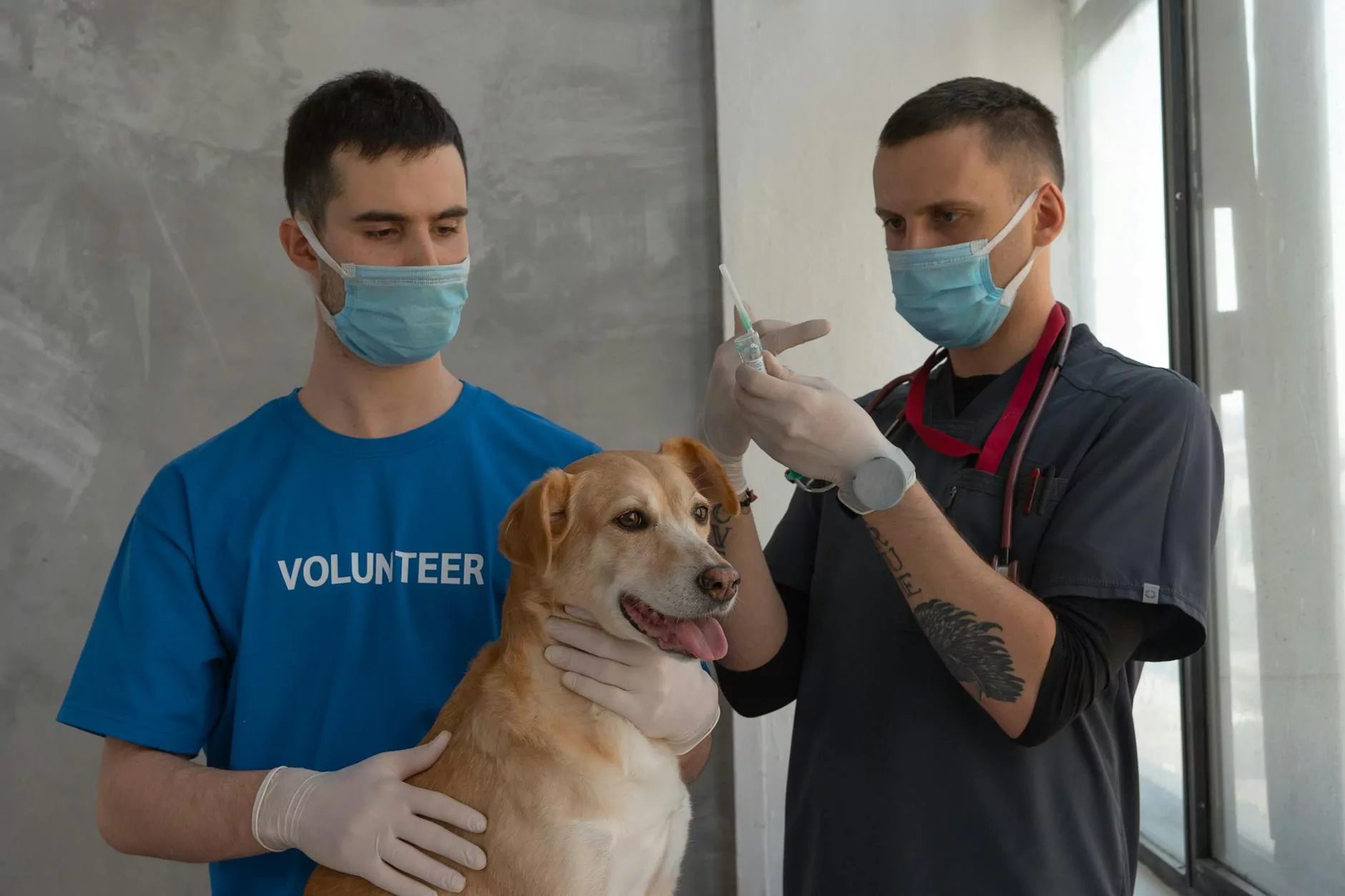
Injection molding is a pivotal manufacturing process widely used in various industries to produce plastic parts and products. The growing demand for efficiency, precision, and quality in manufacturing has made injection molding manufacturers a critical component in the supply chain of numerous sectors, including automotive, consumer goods, healthcare, and electronics.
The Role of Injection Molding Manufacturers
Injection molding manufacturers specialize in designing and producing molds that form raw plastic into highly detailed and complex shapes, optimized for functionality and aesthetics. The significance of these manufacturers cannot be overstated, as they ensure the production of high-quality parts that meet strict industry standards.
Why Choose Injection Molding?
- High Efficiency: Injection molding is one of the fastest manufacturing processes, capable of producing thousands of identical parts in a short timeframe.
- Consistency and Precision: This method guarantees uniformity in product dimensions, which is crucial for parts that need to fit together.
- Cost-Effectiveness: While the initial setup costs, including mold creation, can be high, the per-unit cost drops significantly as production scales.
- Material Versatility: A wide variety of plastics can be used in injection molding, allowing manufacturers to select materials that meet specific performance requirements.
The Injection Molding Process
The process of injection molding can be broken down into several key stages:
- Material Selection: Choosing the right plastic resin is the first step, based on the properties required for the final product.
- Mold Design: This includes creating a precise mold that corresponds to the desired shape of the final product, taking into consideration factors like draft angles and cooling channels.
- Injection: The selected resin is heated until it melts and is then injected into the mold under high pressure.
- Cooling: The melted plastic cools and solidifies in the mold, taking on its final shape.
- Ejection: Once cooled, the mold opens, and the finished product is ejected.
Factors to Consider When Choosing Injection Molding Manufacturers
Selecting the right injection molding manufacturers is crucial for the success of your project. Here are some key factors to consider:
1. Experience and Expertise
Look for manufacturers with a proven track record and experience in the specific type of manufacturing you require. Experienced manufacturers are more likely to understand the nuances of various plastics and their behaviors during the molding process.
2. Technology and Equipment
Advanced machinery can make a significant difference in the quality and speed of production. Ensure that the manufacturer uses state-of-the-art injection molding machines and technology to produce high-quality results.
3. Quality Assurance
A reputable manufacturer should have robust quality control procedures in place. This includes inspections at various stages of production to ensure that every product meets the required specifications.
4. Customer Support and Communication
Good customer service is vital for a successful partnership. Choose a manufacturer that values communication and is willing to collaborate closely with you throughout the process.
5. Pricing Structure
While price should not be the sole factor in your decision, it is essential to consider your budget and the pricing structure of potential manufacturers. Be wary of any quotes that seem too good to be true, as they may reflect lower quality or hidden costs.
Innovations in Injection Molding
The injection molding industry is continuously evolving, with new technologies and methods enhancing the process. Some of these innovations include:
1. 3D Printing and Rapid Prototyping
Many manufacturers are now using 3D printing technologies to create prototype molds more efficiently. This allows for quicker testing and adjustments before committing to full-scale production.
2. Improved Materials
Advancements in plastic materials have led to stronger, lighter, and more sustainable options. Manufacturers can now choose from a broad range of materials, including recycled plastics and biodegradable options.
3. Automation and Smart Manufacturing
Automation in injection molding processes has improved efficiency and reduced labor costs. Smart manufacturing systems enable real-time monitoring and adjustments, ensuring consistent quality and lower waste.
The Future of Injection Molding
As industries demand more sustainable and efficient production methods, the injection molding manufacturers industry is expected to adapt rapidly. Future trends to watch include:
- Sustainability: Increased focus on eco-friendly practices, such as the use of biodegradable materials and reduced energy consumption.
- Customization: Growing demand for customized products, leading to more flexible and agile manufacturing processes.
- Enhanced Collaboration: Improved partnerships between manufacturers, suppliers, and customers through integrated technologies.
Conclusion
In summary, understanding the role and capabilities of injection molding manufacturers is essential for any business looking to harness the benefits of this efficient manufacturing process. Whether you are in the automotive sector, healthcare, or consumer goods, the choice of a reliable manufacturing partner can significantly impact your product's success in the market. By considering factors such as experience, technology, and innovative practices, you can make an informed decision that will benefit your business in the long run.
For more insights and professional guidance on finding the right injection molding solutions for your business needs, consider visiting deepmould.net.